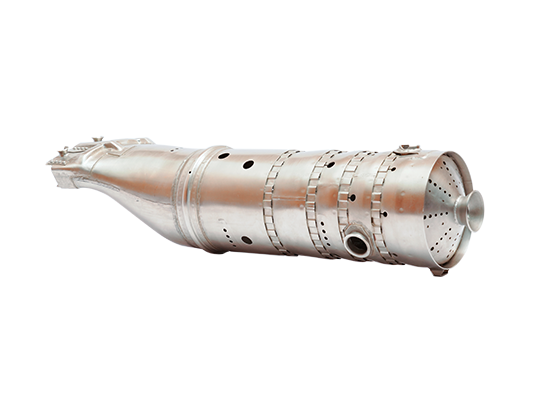
Problems
- Complex Design (complete assembly divided into 32child parts as Primary, Secondary and Dilution sections) Multiple Hole Orientation,
- Greater number of welding at various condition and stages (550 Spot welding, 38 GTAW welding),
- Multiple stages of NDT inspection (Fluorescent penetrant inspection and Radiography inspection) for GTAW welding,
- Intermittent brazing and heat treatment operation, and
- Detailed concept of tooling to archive complex profile and quick assembly time.
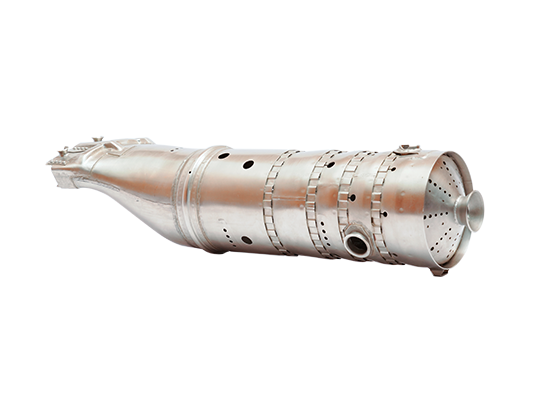
Problems
- Complex Design (complete assembly divided into 32child parts as Primary, Secondary and Dilution sections) Multiple Hole Orientation,
- Greater number of welding at various condition and stages (550 Spot welding, 38 GTAW welding),
- Multiple stages of NDT inspection (Fluorescent penetrant inspection and Radiography inspection) for GTAW welding,
- Intermittent brazing and heat treatment operation, and
- Detailed concept of tooling to archive complex profile and quick assembly time.
Opportunities or Solutions Delivered
The project started with thorough input study, gap analysis and identification of potential failures as per customer blueprint requirements. The team created a detailed process design that included:
- Process flow diagram,
- Stage-wise manufacturing process consiting of individual part, sub-assembly, and assembly with process-controlled tools with poke yoke mechanism,
- Stage-wise inspection gauges to control CTQ,
- Control plan linking manufacturing process step to key inspec on,
- Developing complete welding cell, training, and qualifying a welding operator,
- Establishing and qualifying source for brazing and heat treatment process.
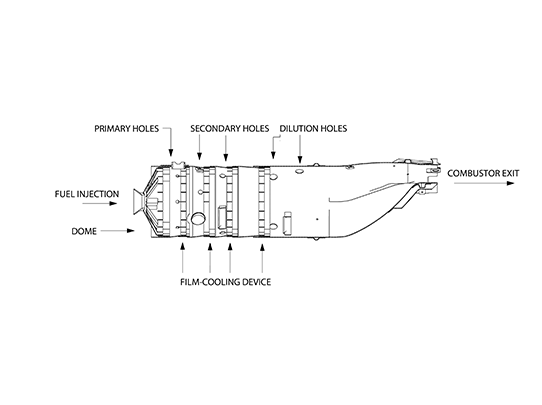
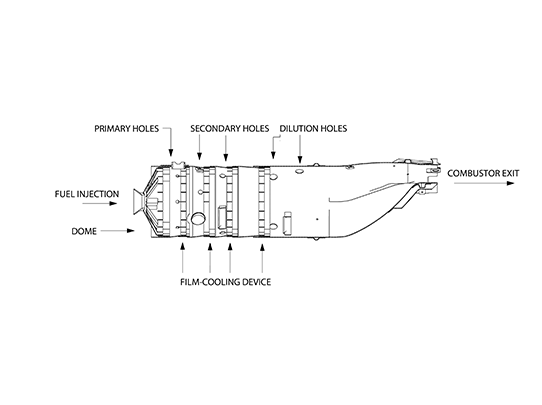
Opportunities or Solutions Delivered
The project started with thorough input study, gap analysis and identification of potential failures as per customer blueprint requirements. The team created a detailed process design that included:
- Process flow diagram,
- Stage-wise manufacturing process consiting of individual part, sub-assembly, and assembly with process-controlled tools with poke yoke mechanism,
- Stage-wise inspection gauges to control CTQ,
- Control plan linking manufacturing process step to key inspec on,
- Developing complete welding cell, training, and qualifying a welding operator,
- Establishing and qualifying source for brazing and heat treatment process.
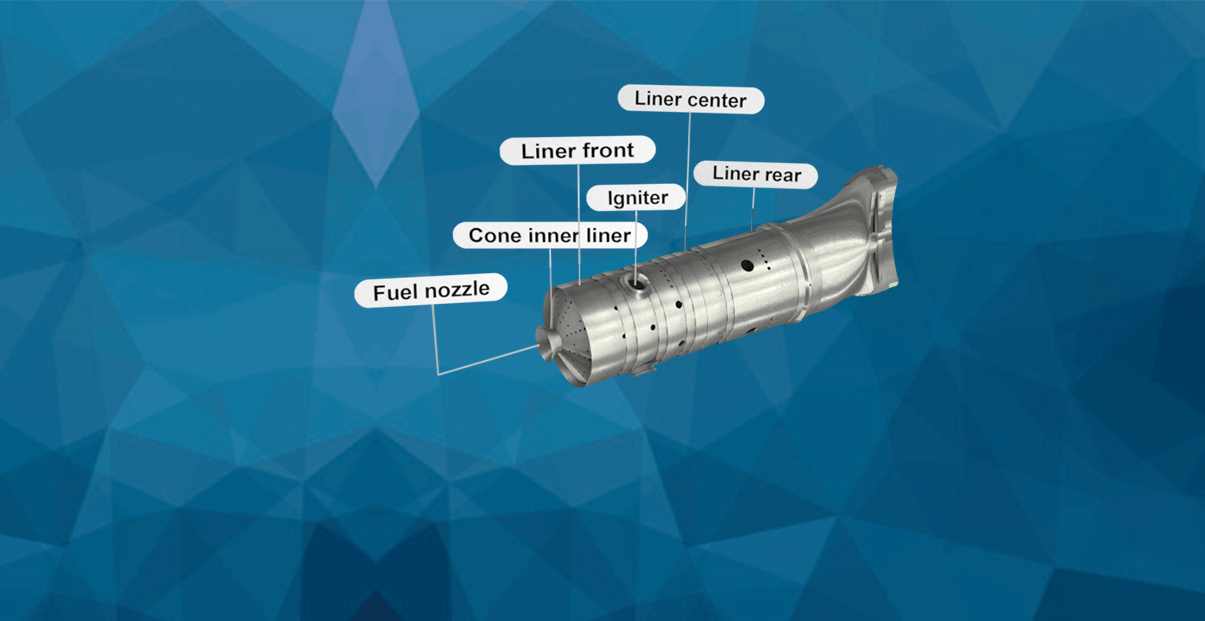
Impact created
Impact created
- Delivered first FAI in six months.
- Successfully delivered 2500 units.
- Developed complex engine sheet metal fabrication facility with NADCAP certification.